We the Vishwakarma Automotive Pvt. Ltd. leader in Machine and Automotive Products With quality components delivered to its valued customers and manufactured by exceptional technology which is an epitome of quality, precision, and perfection for all products which are being used in different sector like automobile, machinery manufacture, railway sector, agriculture, and various industries and certified as TS 16949 & ISO 14001.
We offer high quality and standard, customized top-quality Casting products, precision Steering & Suspension, Fabrication & Sheet Metal, Shaft Assemblies Transmission Lever and Pivot Pins for various applications.
“THE DIE CASTING
INDUSTRY IS INNOVATIVE AND ALWAYS
CHANGING”
Die casting is a manufacturing process that can produce geometrically complex metal parts through the use of reusable molds, called dies. Most die casting is used for high volume components for creating dies for individual parts which are being used widely in the automotive industry for various applications. VISHWAKARMA AUTOMOTIVE PVT. LTD. Die Casting components are well known and we are one of the manufacturing industries to provide cost-effective solutions for small to medium industries. As pressure die casting components can be made up of the most popular die-cast alloys like Aluminum, Zinc, Magnesium, Brass, and Copper. Some material has low strength while some of them have high strength and these materials create a finished product with rigidity and high quality.
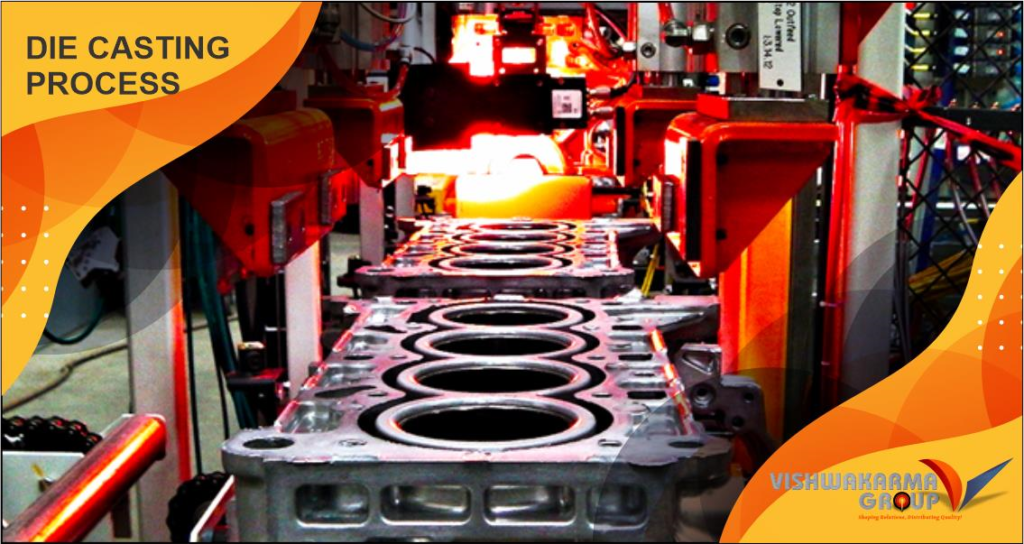
➢ Die casting process-
Molten metal is injected into the cavity under high pressure filling thin walls and small features. If metal has low melting temperatures such as zinc then hot chamber machines are used and if alloys have high melting temperatures like aluminum then Cold chamber machines are used. The metal solidifies very quickly and the die is opened to eject the casting. The tooling can be single or multi-cavity depending on part size and quantity requirements then die or mold is fabricated with the impression of the component. Expected tool life can vary based on the tooling material and part geometry. Let’s have a look in types of die casting.
- Single cavity to produce one component
- Multiple cavities to produce a number of identical parts
- Unit die to produce different parts at one time
- Combinations die to produce several different parts for an assembly
Over 30 Years of Experience in Die Casting Innovation!!
➢ Die casting phases
- Clamping
- Injection
- Cooling
- Ejection
- Trimming
In pressure die casting process a molten metal alloy injected under high pressure into a steel mold. When it comes to pressure die casting then it is a quick, reliable and cost-effective manufacturing process for the production of high volume, metal components used in different automotive industries that are well-shaped with tight tolerances.
➢ We lead the globe with our high-quality die casting components
- Die casting eliminates the cost of labor with longer service life, dimensional accuracy.
- High-quality production in a short time.
- Fine surface quality & Tight tolerances
- Advanced production speed & Extended tool life.
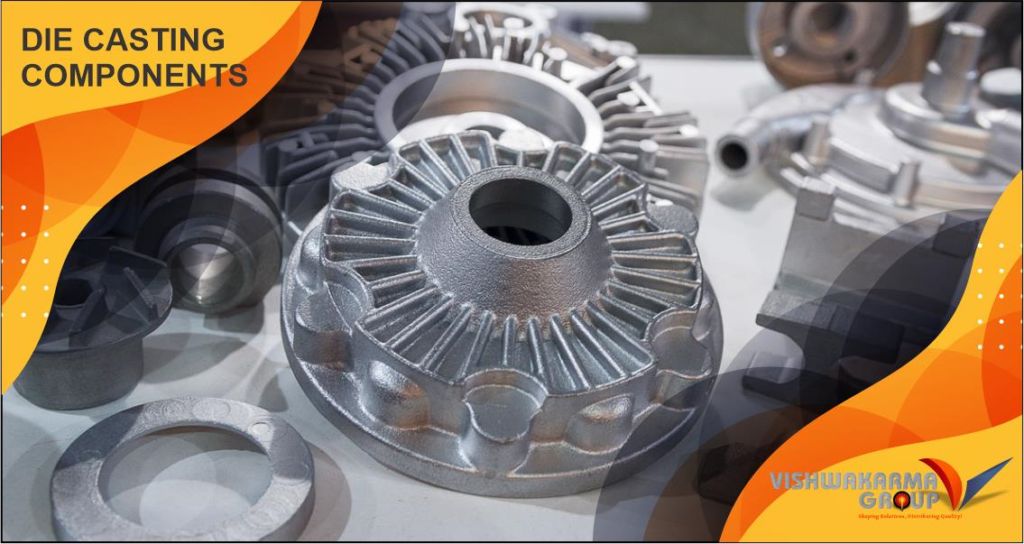
➢
Application of Pressure Die Casting
- Automotive parts-
wheels, blocks, cylinder
heads. - Aerospace castings
- Electric motor housings
- Electronic Industry
- Automotive industry
We at the Vishwakarma industry look at product tolerances differently. Our level of quality both meets and exceeds industry standards. With the help of world-class testing facilities for steering and suspension parts our products are highly tested and qualified and are more competitive in the global market. we assess the form of the part, the proximity of the feature within the tool, and its relation to other features on the part. Our die casting service is offered through a strategic R & D and highly qualified engineered team. Our pressure die casting parts are more durable and have highly efficient quality.